“We feed the world from right here in Chehalis,” says Brad Wilson, Plant Superintendent and Packaging Manager for National Frozen Foods. Western Washington is not the growing region it once was. Today, most of the crops come from Eastern Washington. So in order for National Frozen Foods to stay in business in Chehalis, they need to be one of the best. And they are.
Of their four plants in Moses Lake, Quincy, Chehalis and Albany, Oregon – Chehalis is the largest, doing about 70 percent of the company’s total volume. The Chehalis plant packages 270 million pounds of food each year and ships it all over the world. Just how do they do it? Brad says it’s about keeping up with technology and safety regulations and having the right employees. That’s the secret of their success.
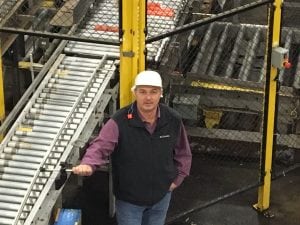
Photo credit: Kristina Lotz
Brad has worked for National Frozen Foods for almost 40 years. He started when he was just 16-years-old in packaging and has worked his way up to where he is now. Over the last forty years, he has watched the packing room evolve as technology came out.
“In our business, we probably have one of the most automated packaging rooms in the Northwest,” Brad says. “I’ve been to New York and been to other plants and I hear a lot of other plants are chasing us in terms of innovation. And that’s how I want it. That’s been our goal.” They also are one of the few plants that has a temperature-controlled (chilled) packing floor, which has brought them more business.
When he first started, he remembers taking orders by phone and writing them on a piece of paper. Back then, they were doing 50 to 70 million pounds a year. Now, everything is done through computers and a customer service representative. The packing building itself has expanded three times to accommodate the growing output.
Employee and food safety are always a driving force when Brad is choosing the next upgrade to his equipment. The company has security doors going into the packing floor and everyone is expected to wear safety helmets as well as food handling protection – gloves, aprons, hairnets, etc. As a result, Chehalis’s National Frozen Foods plant is one of the cleanest plants you will ever see.
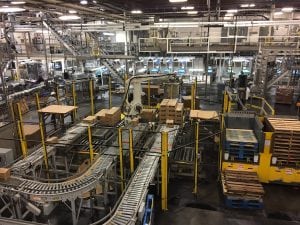
Photo credit: Kristina Lotz
Many of their upgrades to the equipment are for health and safety as well as efficiency. For example, they recently upgraded a sorter to a new one that has no water build-up for increased cleanliness. The scale on that machine that weighs the amount food going into each package is accurate to a gram. When Brad first started, he said the machines were over four to five grams, a big difference when it comes to how much food you are giving away for free.
Every product goes through a color sorter, metal detector and quality control checkers. In addition, every half hour, a bag on each line is removed and checked for quality control. These are just a few ways they make sure the food they are packing is fresh, clean and safe for consumers.
Brad is spending a week in New Orleans receiving training about the new federal food regulations and how to make plants more hygienic. It’s just one more way National Frozen Food makes sure their people and their equipment are the best available.
Exceptional Employees
The other key is their employees, says Brad. The technology is only as good as the people who are running it.
“It’s a proven fact – our people are our company,” he says. “They are incredible.” And the feeling must be mutual. National Frozen Foods has an amazing retention – Brad is not the only one who has worked there his whole life. Many of their employees have been there 20-plus years. Rodney Green has worked at National Foods for going on 44 years! Many employees have sons and daughters that now work there as well.
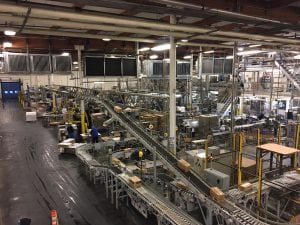
Photo credit: Kristina Lotz
One of the big innovations the company added is a robot arm that stacks the full boxes on the pallets. However, it’s not as simple as just buying the equipment and dropping it in the warehouse. They have to make it work with their production lines and the space they have. This is where the excellence of Brad and his team come into play. They had to construct a bridge overhead to get one of the lines to the robot without blocking the path of people and forklifts that need to move around the floor.
And while their ordering system is now computerized, it still takes people to plan the schedule so that they do not run out of or have too much of any one product. “A perfect scenario is a 12-month cycle,” Brad explains. “They plant this many acres of peas because my customers want X amount. And then we want to run out right when peas start up again the next year.” This type of planning is learned through years of experience at the job. It’s hard to teach and it’s part of what makes National Frozen Foods’ employees so valuable.
Whether you’re looking for a top-of-the line repacking company or a new career, you can’t get much better than our very own National Frozen Foods in Chehalis.
For more information about National Frozen Foods, visit their website.
Sponsored